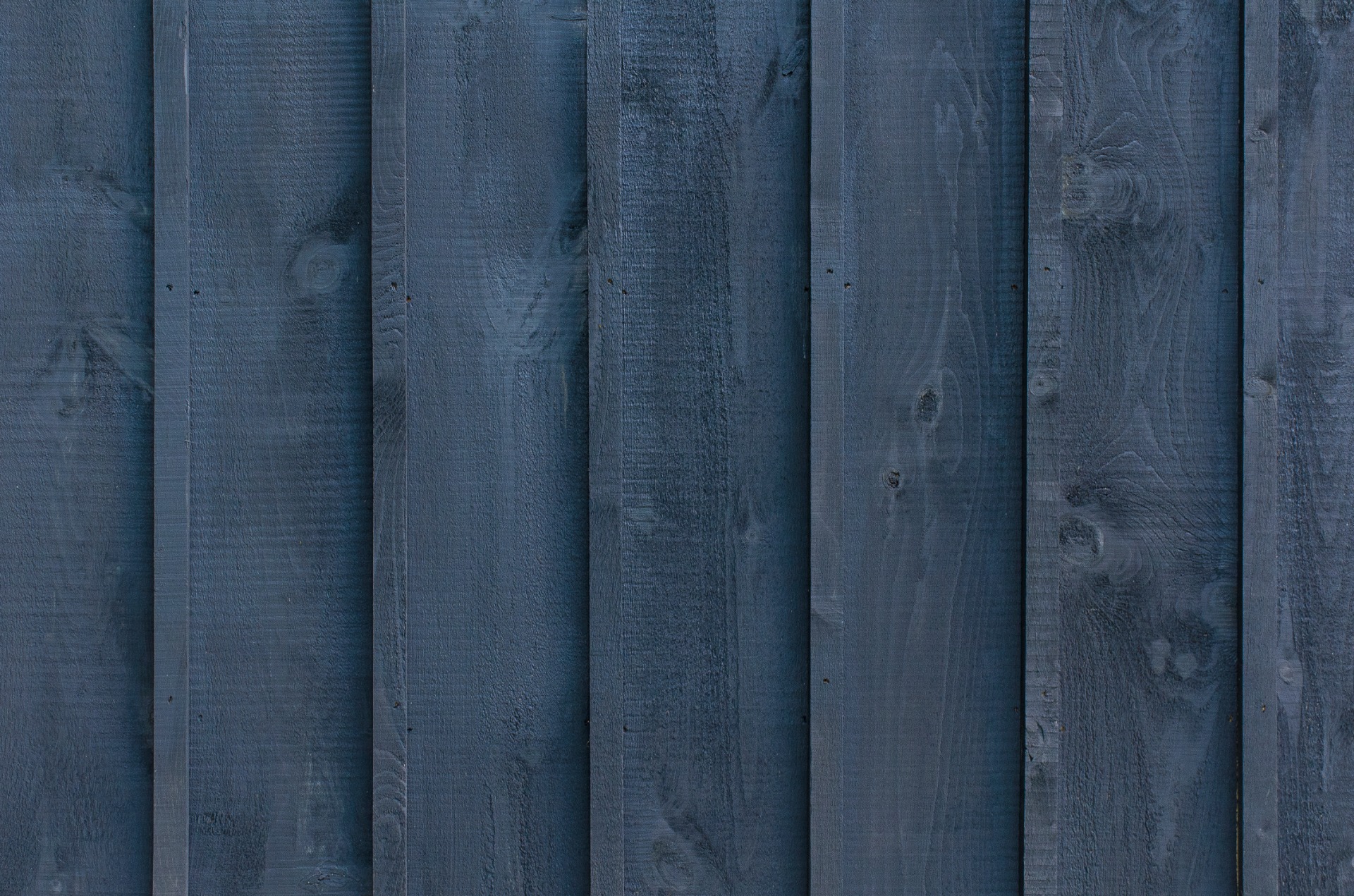
SIP technology
SIP panel technology is far from being brand new in the world. Its origins date back to the Forest Products Laboratory in the United States of America in 1930. The Forest Products Laboratory (FPL) has been founded by the US government for the purpose of developing new technology to help protect the limited natural resources. The FPL started research and experiments in 1935. The first panels were manufactured of corrugated cardboard, sandwiched between plywood and aluminium sheets. Being a saver of natural resources, these panels became increasingly popular.
SIP panels achieved a major breakthrough in 1973, after the global oil crisis. With increased energy costs, builders turned their attention to SIP panel buildings, which required very little energy.
This resulted in a wave of SIP panel use all over USA, later followed by Canada, Europe, and the rest of the world.
Currently SIP buildings are popular all over the world, ranging from Alaska to New Zealand. In Alaska, SIP houses comply with the highest – 6th – energy efficiency classification standard. In Europe, these houses became particularly popular since 1995 and their popularity has been growing ever since. Countries like Norway, Sweden and Denmark, known for cold and humid climate, value SIP panel buildings for their thermal insulation properties. Southern European countries love SIP panel technology for its ability to keep the interior cool.
SIP – Structured Insulated Panel production technology enables to build a strong and reliable house at low costs and in a short time.
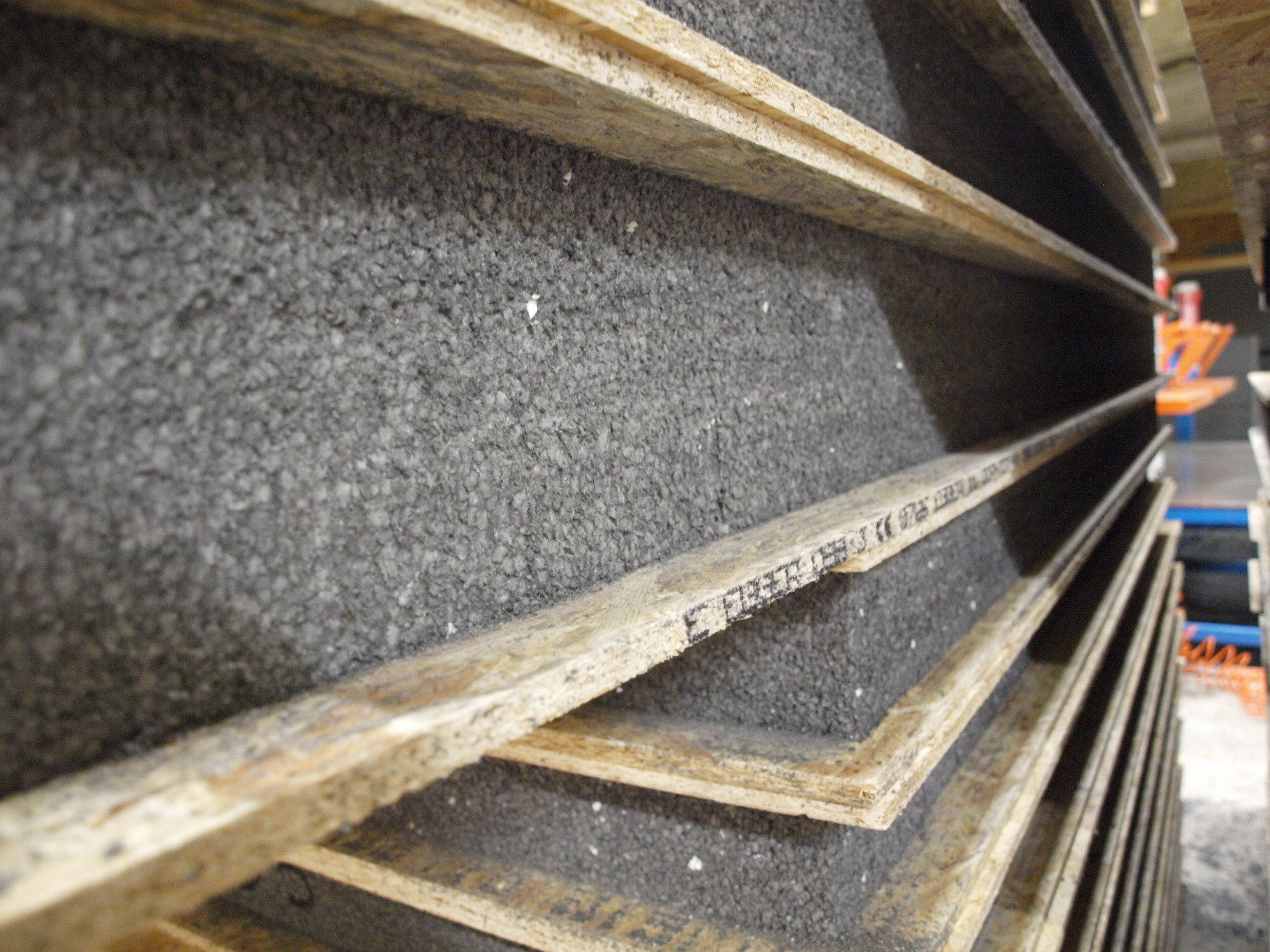
SIP panels
SIP panels are known for being particularly strong and light. The panels consist of three layers: OSB + insulation. Our SIP panel factory uses polystyrene foam. In terms of technical heat retention qualities, this insulating layer is superior to many other materials.
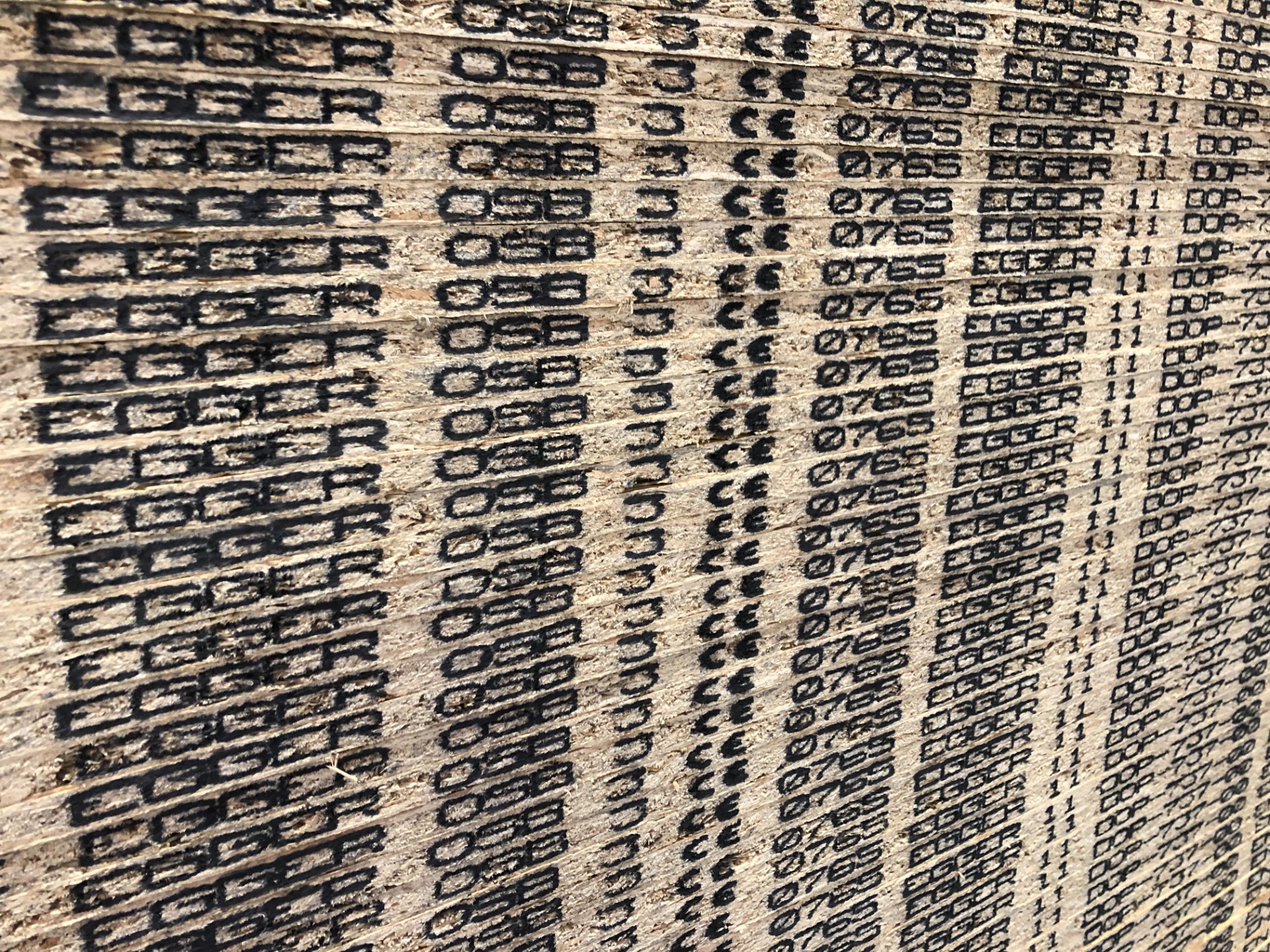
OSB panels
OSB (oriented strand boards) are made of pine or leafy wood chips, arranged in three layers in different directions and compressed under high pressure and temperature using wood resin and modern polyisocyanate glue (MDI). Interacting with the hydrogen in the wood, this glue forms polyurethane, which in turn makes the panel durable and strong. OSB panels are known for their longevity, resistance to moisture and simple processing.
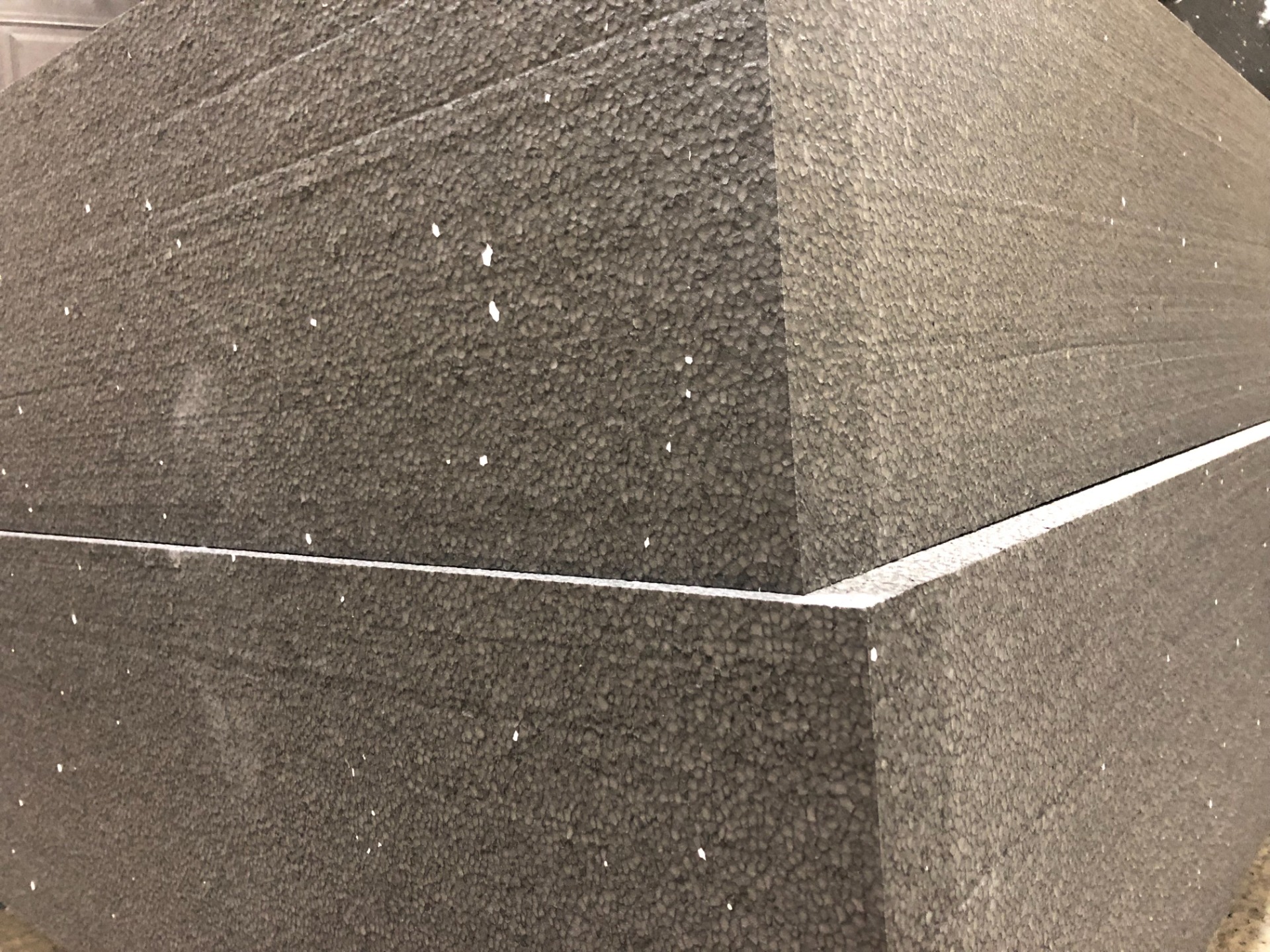
Polystyrene foam
Polystyrene foam is a porous structure consisting of 98% air and 2 percent polystyrene. Polystyrene is known for excellent thermal insulation qualities, it is wind-resistant and cannot be affected by weather conditions and humidity in any way. Also known for hypoallergenic properties, longevity and being completely unattractive for bacteria, mould and rodents, polystyrene foam is harmless to the environment and human health. Its light weight and insulation qualities make it the perfect SIP panel filling.
During the SIP panel production, all three layers – OSB-polystyrene foam-OSB – are sandwiched using polyurethane glue, which is particularly resistant to moisture, fire, and completely harmless. SIP panels are produced indoors using special equipment. All three SIP layers are placed in a special machine to be pressed and held together until the glue completely penetrates the panel and cures. The entire manufacturing process is protected from all weather conditions and free of moisture, ensuring highest-quality SIP panels.